Stationary metal bellows seals as we know them today were developed as part of a seal reliability program at Exxon’s Baton Rouge refinery in the 1970s. The Exxon “Pump Team” was not satisfied with reliability and performance of seals in hot oil services because the oils decomposed and locked rotating flexible sealing elements in place. Beginning in January 1976, prototype stationary metal bellows seals were designed, manufactured and assembled by the Exxon Pump Team using parts from various seal manufacturers fitted into custom assemblies manufactured in the Exxon machine ship.
I know this for a certainty because I was there and took an active part in this project. The Pump Team, led by Charles Miannay, included John Eeds, Ory Duran, Ed Labat and myself.
In the 1970s, the Exxon refinery still had many pumps using packing – especially the hotter pumps. Pumps were being converted from packing to mechanical seals almost daily in an effort to increase reliability. Hot pumps were a definite challenge and required a metal bellows to attain the necessary temperature rating. For the most part, the refinery was using Chempro (now Sealol) Type 605 rotating metal bellows seals in hot services. These designs were highly customized to fit the particular pump and often the bellows was welded directly onto the shaft sleeve. Even so, the Mean Time Between Repairs was only about 3 to 6 months unless a cold external flush (Plan 32) was injected into the seal chamber. Plan 32 was expensive to install and operate and was not desirable.
The Pump Team standard procedure was to do a detailed failure analysis on all pumps that were repaired in the repair shop. Although almost all of the seals were rotating spring seals, we began to notice that stationary seals often seemed to be more reliable. One day, we were examining a high temperature Borg-Warner (now Flowserve) Type H seal that, according to our records, had served for several years in a high temperature service. Although the Type H was a pusher seal, it was mounted stationary and used an asbestos U cup gasket. We could not get parts for the Type H so it was replaced with a Chempro (became Sealol) Type 606 which was a new product developed by Chempro to be more adaptable; however, the Type 606 was a rotating bellows seal. The Type 606 lasted only a few weeks. On examining the Type 606, it was found to have become extremely “coked up” and therefore inflexible.
We asked several seal OEMs about stationary high temperature seals but there was little interest and no one had anything to offer. Therefore, we determined to build a prototype stationary metal bellows seal ourselves. Sketches were made of both low and high temperature conceptual designs.
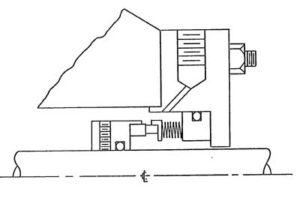
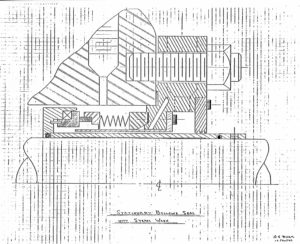
Notice that the high temperature stationary metal bellows design included a “steam baffle”. We borrowed this idea from a Borg-Warner rotating seal design and extended the baffle for our stationary conceptual design.
The very first prototype high temperature metal bellows seal wasdesigned and assembled by John Eeds. It used a Chempro Type 606 as the stationary bellows and a Chempro “floating seat” as a rotating mating ring. A flat Graphoil gasket with tiny holes was tedious fitted to the back of the Type 606 so that it could be bolted to the gland plate. We tried many variations of the concept. The greatest difficult was fastening and sealing the bellows to the gland plate. The photo below (Figure 3) is of a prototype that I designed using the Crane 15W as the bellows. It also used the Chempro floating seat. In all cases, the design was sketched by either John or myself and all parts except the bellows and mating ring were machined in the Exxon shop.
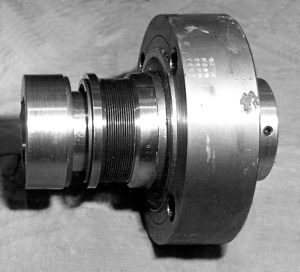
The Exxon Pump Team tested 19 prototypes in many variations before deciding to turn over the designs and results to the seal manufacturers. There was some consideration for seeking a patent but it was thought that commercial development of the concept would be better done by the seal OEMs.
At the time, Exxon Baton Rouge was doing very little business with Borg-Warner Seal Division and Borg-Warner took this opportunity to gain new business. They expressed an interest in making stationary bellows seals and requested a meeting to discuss the Exxon needs. A meeting was arranged with the Pump Team. Borg-Warner attendees were:
- A.L. Dubrow, the new President of Borg-Warner Seal Division
- Oley Giles, Borg-Warner Chief Engineer
- Jim Moore, Baton Rouge Sales Manager
- Don Gill, Baton Rouge Salesman
To our surprise, Mr. Dubrow opened his briefcase, removed a stationary bellows seal, placed it on the conference table and asked “How many do you want?” BW/IP had designed their BXR (low temperature) stationary metal bellows seal based on my sketch, see Figure 1. We were stunned. After some discussion and negotiation, Mr. Miannay was able to place an order for several sizes of the BXR. Of course, this purchase quickly gained the attention of other seal manufacturers.
Sealol, previously our primary supplier of bellows seals, soon had a design, the Type 604, for either low or high temperature service. Borg-Warner followed quickly with their BXRH for high temperature service and John Crane produced the Type 15WRS and, eventually, the 315RS.
The stationary bellows seal had been “launched”. Stationary metal bellows seals have proven to be so reliable that the API 682 Task Force chose this design to be the default selection for hot oil services and labelled it the API 682 Type C seal.